วิธีออกแบบชิ้นส่วนพลาสติก
คำอธิบายสั้น:
ถึง ออกแบบชิ้นส่วนพลาสติกคือการกำหนดรูปร่างขนาดและความแม่นยำของชิ้นส่วนโดยพิจารณาจากบทบาทของชิ้นส่วนที่เล่นในผลิตภัณฑ์และกฎของกระบวนการขึ้นรูปสำหรับพลาสติก ผลลัพธ์สุดท้ายคือภาพวาดสำหรับการผลิตแม่พิมพ์และชิ้นส่วนพลาสติก
การผลิตสินค้าเริ่มจากการออกแบบ การออกแบบชิ้นส่วนพลาสติกจะกำหนดโครงสร้างภายในต้นทุนและหน้าที่ของผลิตภัณฑ์โดยตรงและยังกำหนดขั้นตอนต่อไปของการผลิตแม่พิมพ์ต้นทุนและวงจรตลอดจนกระบวนการฉีดขึ้นรูปและกระบวนการหลังการแปรรูปและต้นทุน
ชิ้นส่วนพลาสติกถูกนำมาใช้อย่างแพร่หลายในผลิตภัณฑ์สิ่งอำนวยความสะดวกต่างๆและการใช้ชีวิตของผู้คนในสังคมสมัยใหม่ ชิ้นส่วนพลาสติกต้องการรูปร่างและหน้าที่แตกต่างกัน พวกเขาใช้วัสดุพลาสติกและคุณสมบัติของมันก็แตกต่างกันไป ในขณะเดียวกันก็มีหลายวิธีในการทำชิ้นส่วนพลาสติกในอุตสาหกรรม ดังนั้นการออกแบบชิ้นส่วนพลาสติกจึงไม่ใช่เรื่องง่าย
การออกแบบชิ้นส่วนและวัสดุที่แตกต่างกันนั้นมีการประมวลผลที่แตกต่างกัน กระบวนการขึ้นรูปพลาสติกส่วนใหญ่มีดังนี้:
1. การฉีดขึ้นรูป
2. เป่าปั้น
3. การบีบอัด
4. การปั้นแบบหมุน
5. เทอร์โมฟอร์ม
6. การอัดขึ้นรูป
7. การผลิต
8. โฟม
มีหลายวิธีในการผลิตจำนวนมาก การฉีดขึ้นรูปเป็นวิธีการผลิตที่ได้รับความนิยมเนื่องจากชิ้นส่วนพลาสติกฉีดขึ้นรูป 50% ~ 60% ผลิตโดยการฉีดขึ้นรูปด้วยการฉีดขึ้นรูปจึงเป็นความสามารถในการผลิตที่มีความเร็วสูง
แสดงเคสสำหรับชิ้นส่วนพลาสติกบางส่วนที่เราออกแบบ:
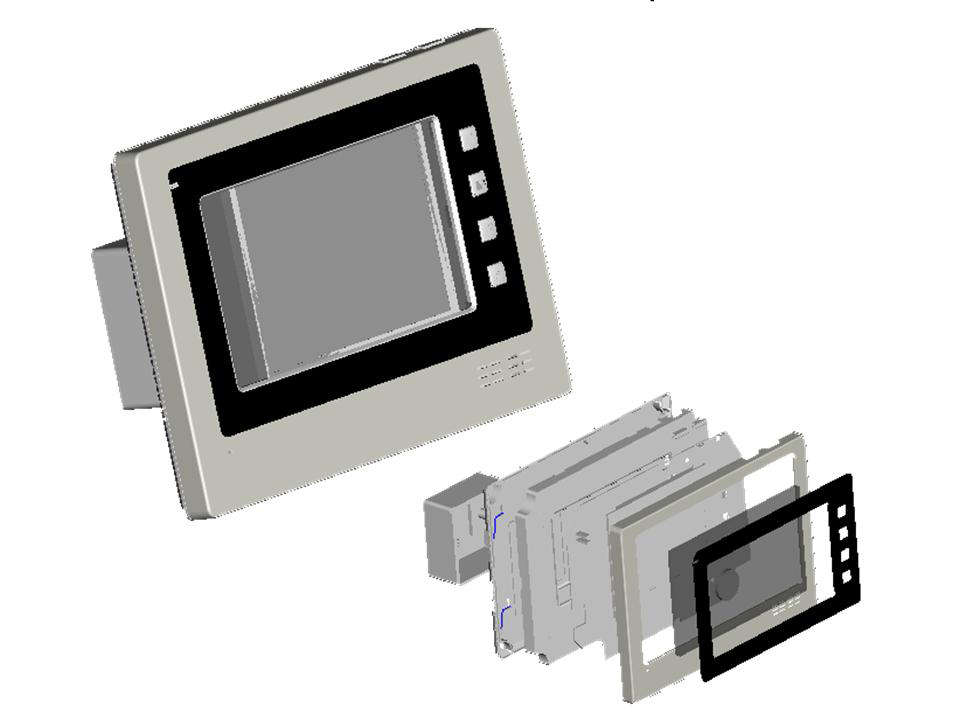
กล่องพลาสติกของโทรศัพท์วิสัยทัศน์
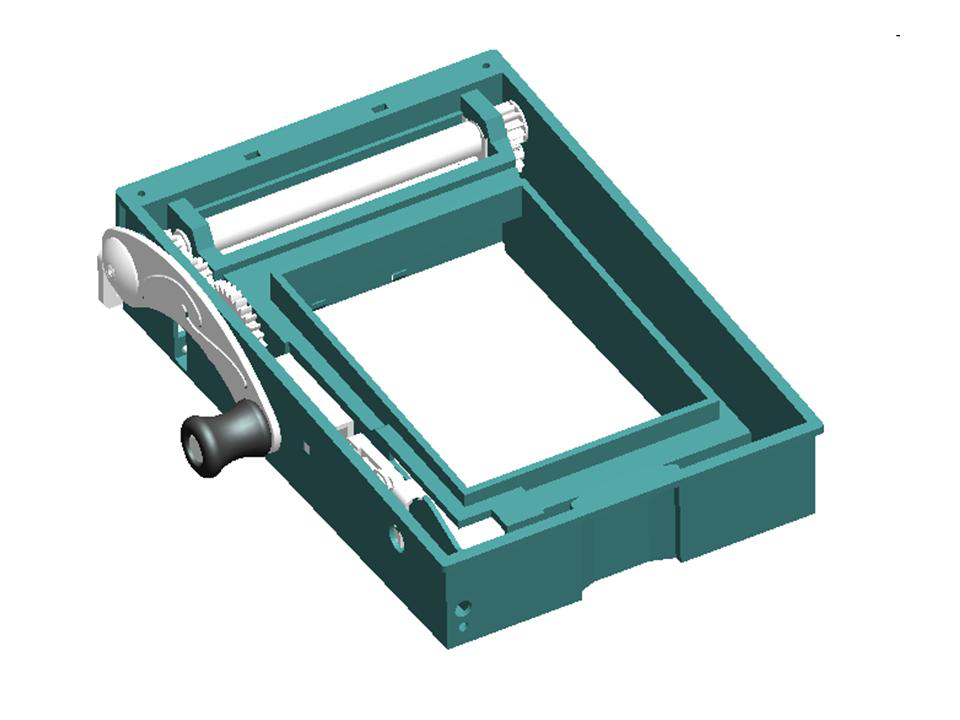
ชิ้นส่วนพลาสติกของกลไก
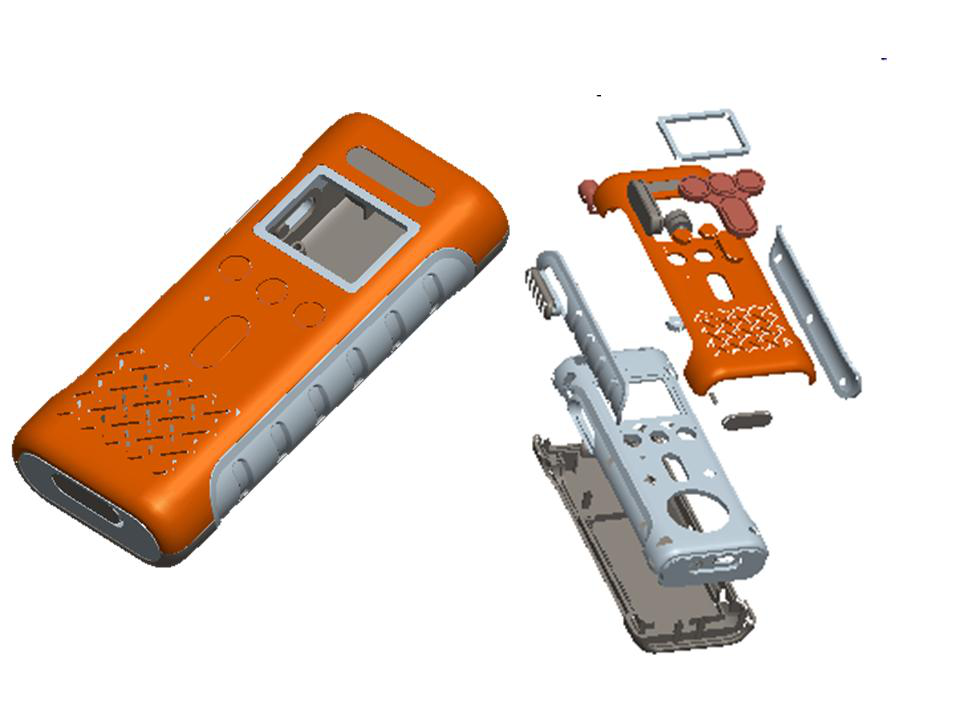
กล่องพลาสติกอิเล็กทรอนิกส์
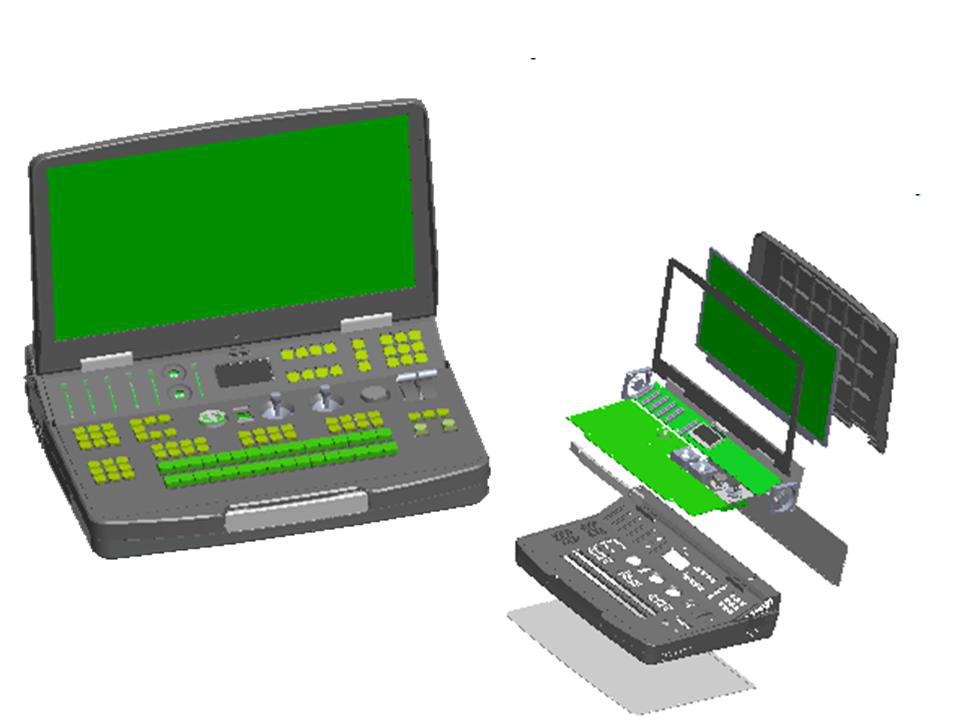
ตัวเครื่องพลาสติกสำหรับเครื่องดนตรี
ด้านล่างนี้เราจะแบ่งปันรายละเอียดวิธีการออกแบบชิ้นส่วนพลาสติกใน 3 ด้าน
* 10 เคล็ดลับในการออกแบบชิ้นส่วนพลาสติกที่คุณต้องรู้
1. กำหนดรูปลักษณ์และขนาดของผลิตภัณฑ์
นี่เป็นขั้นตอนแรกในกระบวนการออกแบบทั้งหมด ตามการวิจัยตลาดและความต้องการของลูกค้ากำหนดลักษณะและหน้าที่ของผลิตภัณฑ์และกำหนดงานพัฒนาผลิตภัณฑ์
ตามภารกิจการพัฒนาทีมพัฒนาจะดำเนินการวิเคราะห์ความเป็นไปได้ทางเทคนิคและเทคโนโลยีของผลิตภัณฑ์และสร้างแบบจำลองลักษณะ 3 มิติของผลิตภัณฑ์ จากนั้นตามการสร้างฟังก์ชันและการประกอบผลิตภัณฑ์จะมีการวางแผนชิ้นส่วนที่เป็นไปได้
2. แยกชิ้นส่วนแต่ละชิ้นออกจากแบบผลิตภัณฑ์เลือกประเภทเม็ดพลาสติกสำหรับชิ้นส่วนพลาสติก
ขั้นตอนนี้คือการแยกชิ้นส่วนออกจากแบบจำลอง 3 มิติที่ได้รับในขั้นตอนก่อนหน้าและออกแบบเป็นรายชิ้น ตามความต้องการในการใช้งานของชิ้นส่วนให้เลือกวัตถุดิบพลาสติกหรือวัสดุฮาร์ดแวร์ที่เหมาะสม ตัวอย่างเช่นมักใช้ ABS ในไฟล์
เปลือก ABS / BC หรือ PC จำเป็นต้องมีคุณสมบัติเชิงกลบางอย่างชิ้นส่วนโปร่งใสเช่นโป๊ะโคมโพสต์ PMMA หรือ PC เกียร์หรือชิ้นส่วนที่สึกหรอ POM หรือไนลอน
หลังจากเลือกวัสดุของชิ้นส่วนแล้วสามารถเริ่มการออกแบบรายละเอียดได้
3. กำหนดมุมร่าง
มุมแบบร่างช่วยให้สามารถดึงพลาสติกออกจากแม่พิมพ์ได้ หากไม่มีมุมร่างชิ้นส่วนจะมีความต้านทานอย่างมีนัยสำคัญเนื่องจากแรงเสียดทานระหว่างการถอดออก มุมแบบร่างควรอยู่ด้านในและด้านนอกของชิ้นส่วน ยิ่งส่วนลึกเท่าไหร่มุมร่างก็จะยิ่งใหญ่ขึ้น หลักการง่ายๆคือต้องมีมุมร่าง 1 องศาต่อนิ้ว การมีมุมร่างไม่เพียงพออาจส่งผลให้เกิดรอยขูดตามด้านข้างของชิ้นส่วนและ / หรือเครื่องหมายพินอีเจ็คเตอร์ขนาดใหญ่ (เพิ่มเติมในภายหลัง)
มุมร่างของพื้นผิวภายนอก: ยิ่งส่วนลึกเท่าใดมุมร่างก็จะยิ่งใหญ่ขึ้น หลักการง่ายๆคือต้องมีมุมร่าง 1 องศาต่อนิ้ว การมีมุมร่างไม่เพียงพออาจส่งผลให้เกิดรอยขูดตามด้านข้างของชิ้นส่วนและ / หรือเครื่องหมายพินอีเจ็คเตอร์ขนาดใหญ่ (เพิ่มเติมในภายหลัง)
โดยปกติแล้วเพื่อให้มีพื้นผิวที่ดูดีพื้นผิวจะถูกสร้างขึ้นบนพื้นผิวของชิ้นส่วน ผนังที่มีพื้นผิวขรุขระมีแรงเสียดทานมากและไม่สะดวกที่จะเอาออกจากโพรงดังนั้นจึงต้องใช้มุมวาดที่ใหญ่กว่า พื้นผิวที่หยาบกว่าคือมุมการร่างที่ใหญ่กว่า
4. กำหนดความหนาของผนัง / ความหนาสม่ำเสมอ
ไม่ต้องการการขึ้นรูปแบบทึบในการฉีดขึ้นรูปเนื่องจากสาเหตุต่อไปนี้:
1) เวลาในการทำความเย็นเป็นสัดส่วนกับกำลังสองของความหนาของผนัง เวลาในการระบายความร้อนที่ยาวนานสำหรับของแข็งจะเอาชนะเศรษฐกิจของการผลิตจำนวนมาก (ตัวนำความร้อนไม่ดี)
2) ส่วนที่หนากว่าจะหดตัวมากกว่าส่วนทินเนอร์ซึ่งจะทำให้เกิดการหดตัวที่แตกต่างกันซึ่งส่งผลให้เกิดการบิดงอหรือเครื่องหมายจมเป็นต้น (ลักษณะการหดตัวของพลาสติกและลักษณะ pvT)
ดังนั้นเราจึงมีกฎพื้นฐานสำหรับการออกแบบชิ้นส่วนพลาสติก ความหนาของผนังเท่าที่จะเป็นไปได้ควรสม่ำเสมอหรือคงที่ตลอดทั้งส่วน ความหนาของผนังนี้เรียกว่าความหนาของผนังเล็กน้อย
หากมีส่วนที่เป็นของแข็งในชิ้นส่วนนั้นควรทำให้กลวงโดยการนำแกน ควรมีความหนาของผนังสม่ำเสมอรอบแกน
3) ข้อพิจารณาในการตัดสินใจเลือกความหนาของผนังมีอะไรบ้าง?
ต้องหนาและแข็งพอสำหรับงาน ความหนาของผนังอาจเป็น 0.5 ถึง 5 มม.
นอกจากนี้ยังต้องบางพอที่จะทำให้เย็นได้เร็วขึ้นทำให้น้ำหนักชิ้นส่วนลดลงและผลผลิตสูงขึ้น
ความหนาของผนังที่เปลี่ยนแปลงไปควรมีให้น้อยที่สุด
ชิ้นส่วนพลาสติกที่มีความหนาของผนังแตกต่างกันจะพบอัตราการทำความเย็นและการหดตัวที่แตกต่างกัน ในกรณีเช่นนี้การบรรลุความอดทนอย่างใกล้ชิดนั้นยากมากและหลายครั้งก็เป็นไปไม่ได้ ในกรณีที่การเปลี่ยนแปลงความหนาของผนังเป็นสิ่งสำคัญการเปลี่ยนระหว่างทั้งสองควรเป็นแบบค่อยเป็นค่อยไป
5. การออกแบบการเชื่อมต่อระหว่างชิ้นส่วน
โดยปกติเราจำเป็นต้องเชื่อมสองเปลือกเข้าด้วยกัน เพื่อสร้างห้องปิดกั้นระหว่างพวกเขาเพื่อวางส่วนประกอบภายใน (ชุดประกอบ PCB หรือกลไก)
ประเภทการเชื่อมต่อปกติ:
1). ตะขอสแน็ป:
การเชื่อมต่อแบบ Snap hooks มักใช้ในผลิตภัณฑ์ขนาดเล็กและขนาดกลาง ลักษณะเฉพาะของมันคือโดยทั่วไปแล้วตะขอสแน็ปจะถูกตั้งไว้ที่ขอบของชิ้นส่วนและสามารถทำให้ขนาดของผลิตภัณฑ์เล็กลงได้ เมื่อประกอบจะปิดโดยตรงโดยไม่ต้องใช้เครื่องมือใด ๆ เช่นไขควงแม่พิมพ์เชื่อมอัลตราโซนิกและอื่น ๆ ข้อเสียคือตะขอสแน็ปอาจทำให้เกิดเชื้อราที่ซับซ้อนมากขึ้น จำเป็นต้องใช้กลไกตัวเลื่อนและกลไกตัวยกเพื่อให้เกิดการเชื่อมต่อแบบ snap hooks และเพิ่มต้นทุนแม่พิมพ์
2). ข้อต่อสกรู:
ข้อต่อสกรูแน่นและเชื่อถือได้ โดยเฉพาะอย่างยิ่งการยึดสกรู + น็อตมีความน่าเชื่อถือและทนทานมากทำให้สามารถถอดชิ้นส่วนหลายชิ้นได้โดยไม่มีรอยแตก การเชื่อมต่อด้วยสกรูเหมาะสำหรับผลิตภัณฑ์ที่มีแรงล็อคขนาดใหญ่และการรื้อถอนหลายครั้ง ข้อเสียคือเสาสกรูใช้พื้นที่มากขึ้น
3). ผู้บังคับบัญชาการติดตั้ง:
การเชื่อมต่อผู้บังคับบัญชาการติดตั้งคือการแก้ไขสองส่วนโดยการประสานงานอย่างแน่นหนาระหว่างผู้บังคับบัญชาและหลุม วิธีการเชื่อมต่อนี้ไม่แข็งแรงพอที่จะอนุญาตให้ถอดชิ้นส่วนผลิตภัณฑ์ได้ ข้อเสียคือความแข็งแรงในการล็อคจะลดลงเมื่อเวลาในการถอดชิ้นส่วนเพิ่มขึ้น
4). การเชื่อมอัลตราโซนิก:
การเชื่อมอัลตราโซนิกคือการใส่ทั้งสองส่วนลงในแม่พิมพ์อัลตราโซนิกและหลอมรวมพื้นผิวสัมผัสภายใต้การทำงานของเครื่องเชื่อมอัลตราโซนิก ขนาดของผลิตภัณฑ์อาจเล็กลงแม่พิมพ์ฉีดค่อนข้างง่ายและการเชื่อมต่อแน่นหนา ข้อเสียคือการใช้แม่พิมพ์อัลตราโซนิกและเครื่องเชื่อมอัลตราโซนิกทำให้ขนาดของผลิตภัณฑ์ไม่ใหญ่เกินไป หลังจากรื้อถอนแล้วจะไม่สามารถใช้ชิ้นส่วนอัลตราโซนิกได้อีก
6. ทางลัด
อันเดอร์คัทคือสิ่งของที่ขัดขวางการกำจัดครึ่งหนึ่งของแม่พิมพ์ อันเดอร์คัทสามารถปรากฏได้ทุกที่ในการออกแบบ สิ่งเหล่านี้เป็นสิ่งที่ยอมรับไม่ได้หากไม่แย่ไปกว่าการขาดมุมร่างในส่วน อย่างไรก็ตาม undercuts บางอย่างมีความจำเป็นและ / หรือหลีกเลี่ยงไม่ได้ ในกรณีเหล่านั้นจำเป็น
undercuts ผลิตโดยชิ้นส่วนเลื่อน / เคลื่อนย้ายในแม่พิมพ์
โปรดทราบว่าการสร้างอันเดอร์คัทนั้นมีค่าใช้จ่ายสูงกว่าเมื่อผลิตแม่พิมพ์และควรประหยัดให้น้อยที่สุด
7. สนับสนุนซี่โครง / Gussets
ซี่โครงในชิ้นส่วนพลาสติกช่วยเพิ่มความแข็ง (ความสัมพันธ์ระหว่างการรับน้ำหนักและการโก่งตัวของชิ้นส่วน) และเพิ่มความแข็งแกร่ง นอกจากนี้ยังช่วยเพิ่มความสามารถในการขึ้นรูปเมื่อพวกมันเร่งการไหลของการหลอมในทิศทางของซี่โครง
ซี่โครงถูกวางตามทิศทางของความเค้นสูงสุดและการโก่งตัวบนพื้นผิวที่ไม่มีลักษณะของชิ้นส่วน การเติมแม่พิมพ์การหดตัวและการดีดออกควรมีผลต่อการตัดสินใจในการจัดวางซี่โครงด้วย
ซี่โครงที่ไม่เข้ากับผนังแนวตั้งไม่ควรจบลงอย่างกะทันหัน การเปลี่ยนไปใช้ผนังเล็กน้อยควรลดความเสี่ยงต่อความเข้มข้นของความเครียด
ซี่โครง - ขนาด
ซี่โครงควรมีขนาดดังต่อไปนี้
ความหนาของซี่โครงควรอยู่ระหว่าง 0.5 ถึง 0.6 เท่าของความหนาของผนังเล็กน้อยเพื่อไม่ให้เกิดรอยจม
ความสูงซี่โครงควรอยู่ที่ 2.5 ถึง 3 เท่าของความหนาของผนังเล็กน้อย
ซี่โครงควรมีมุมร่าง 0.5 ถึง 1.5 องศาเพื่อความสะดวกในการดีดออก
ฐานซี่โครงควรมีรัศมี 0.25 ถึง 0.4 เท่าของความหนาของผนังเล็กน้อย
ระยะห่างระหว่างซี่โครงสองซี่ควรเป็น 2 ถึง 3 เท่า (หรือมากกว่า) ความหนาของผนังเล็กน้อย
8. ขอบรีด
เมื่อสองพื้นผิวมาบรรจบกันจะกลายเป็นมุม ที่มุมความหนาของผนังจะเพิ่มขึ้นเป็น 1.4 เท่าของความหนาของผนังที่ระบุ ส่งผลให้เกิดการหดตัวที่แตกต่างกันและความเค้นในการขึ้นรูปและเวลาในการทำความเย็นที่นานขึ้น ดังนั้นความเสี่ยงของความล้มเหลวในการให้บริการจะเพิ่มขึ้นที่มุมที่คมชัด
ในการแก้ปัญหานี้ควรปรับมุมให้เรียบด้วยรัศมี ควรให้รัศมีภายนอกและภายใน อย่าให้มีมุมแหลมภายในเพราะจะทำให้เกิดรอยแตก รัศมีควรเป็นเช่นที่ยืนยันตามกฎความหนาของผนังคงที่ ควรมีรัศมี 0.6 ถึง 0.75 เท่าของความหนาของผนังที่มุม อย่าให้มีมุมแหลมภายในเพราะจะทำให้เกิดรอยแตก
9. การออกแบบสกรูเจ้านาย
เราใช้สกรูเพื่อยึดเคสครึ่งสองตัวเข้าด้วยกันเสมอหรือยึด PCBA หรือส่วนประกอบอื่น ๆ เข้ากับชิ้นส่วนพลาสติก ดังนั้นสกรูบอสจึงเป็นโครงสร้างสำหรับการขันสกรูเข้าและยึดชิ้นส่วน
สกรูบอสเป็นรูปทรงกระบอก เจ้านายอาจเชื่อมโยงที่ฐานกับส่วนแม่หรืออาจเชื่อมโยงที่ด้านข้าง การเชื่อมด้านข้างอาจส่งผลให้พลาสติกมีความหนาซึ่งไม่เป็นที่ต้องการเนื่องจากอาจทำให้เกิดรอยจมและเพิ่มเวลาในการระบายความร้อน ปัญหานี้สามารถแก้ไขได้โดยการเชื่อมบอสผ่านซี่โครงเข้ากับผนังด้านข้างตามที่แสดงในภาพร่าง บอสสามารถทำให้แข็งได้โดยให้ซี่โครงค้ำยัน
ใช้สกรูกับเจ้านายเพื่อยึดส่วนอื่น ๆ มีประเภทสกรูขึ้นรูปเกลียวและสกรูตัดดอกยาง สกรูขึ้นรูปเกลียวใช้กับเทอร์โมพลาสติกและใช้สกรูตัดเกลียวกับชิ้นส่วนพลาสติกเทอร์โมเซ็ตที่ไม่ยืดหยุ่น
สกรูขึ้นรูปเกลียวผลิตเกลียวตัวเมียบนผนังด้านในของเจ้านายโดยการไหลเย็น - พลาสติกมีการเปลี่ยนรูปในตัวแทนที่จะถูกตัด
สกรูบอสต้องมีขนาดที่เหมาะสมเพื่อทนต่อแรงใส่สกรูและโหลดที่วางบนสกรูที่ใช้งาน
ขนาดของรูที่สัมพันธ์กับสกรูมีความสำคัญอย่างยิ่งต่อความต้านทานต่อการลอกเกลียวและการดึงสกรูออก
เส้นผ่านศูนย์กลางภายนอกของบอสควรมีขนาดใหญ่พอที่จะทนต่อแรงกดของห่วงเนื่องจากการขึ้นรูปเกลียว
Bore มีเส้นผ่านศูนย์กลางใหญ่กว่าเล็กน้อยที่ช่องทางเข้าสำหรับความยาวสั้น ๆ ซึ่งจะช่วยในการค้นหาสกรูก่อนที่จะขับรถเข้าไปและยังช่วยลดความเครียดที่ปลายเปิดของเจ้านาย
ผู้ผลิตพอลิเมอร์ให้แนวทางในการกำหนดขนาดของเจ้านายสำหรับวัสดุของตน ผู้ผลิตสกรูยังให้แนวทางสำหรับขนาดเจาะที่เหมาะสมสำหรับสกรู
ควรใช้ความระมัดระวังเพื่อให้แน่ใจว่ารอยเชื่อมที่แข็งแรงรอบ ๆ สกรูเจาะในบอส
ควรใช้ความระมัดระวังเพื่อหลีกเลี่ยงความเครียดจากการหล่อหลอมของเจ้านายเนื่องจากอาจล้มเหลวภายใต้สภาพแวดล้อมที่ก้าวร้าว
Bore in boss ควรลึกกว่าความลึกของเธรด
10. การตกแต่งพื้นผิว
บางครั้งเพื่อให้ได้รูปลักษณ์ที่ดูดีเรามักจะทำการดูแลเป็นพิเศษบนพื้นผิวของกล่องพลาสติก
เช่นพื้นผิวมันวาวสูงการพ่นสีการแกะสลักด้วยเลเซอร์การปั๊มร้อนการชุบด้วยไฟฟ้าและอื่น ๆ จำเป็นต้องคำนึงถึงในการออกแบบผลิตภัณฑ์ล่วงหน้าเพื่อหลีกเลี่ยงไม่ให้กระบวนการผลิตในภายหลังไม่สามารถทำได้หรือการเปลี่ยนแปลงขนาดที่ส่งผลต่อการประกอบผลิตภัณฑ์